High Radiation Coating Technology
The oil refining industry is one of the most energy intensive industries. Tube furnaces at refineries are the main consumers of energy in the form of gas and liquid fuels; therefore, maintaining a high level of economic efficiency of their work is crucial for the economy of the entire oil refining complex.
Physical and mechanical characteristics of Solcoat composite formulations
Formulation Options | Green solcoat | CroMag Solcoat | Black solcoat | White solcoat | Hi-e solcoat | Hi-e pipes |
Appearance | Matte Green | Light green smooth | Black gray smooth | Light gray smooth | Dark green smooth | Green-gray smooth |
Melting point [ºC] | > 1900 | 1800 | 700 | 1500 | > 1900 | 1870 |
Viscosity (4mm) [s] 1) | thirteen | eleven | eleven | thirteen | 14.6 | 14.6 |
Thermal Expansion [Kt] | 7.2 × 10-6 to 6.4 × 10-5 | 6.4 × 10-6 to 4.8 × 10-5 | 1.1 - 4.3 × 10-5 | 9.3 × 10-6 to 4.8 × 10-5 | 6.9x10-6 to 4.8x10-5 | 9.8 x10-5 |
Thermal conductivity [W / m.K] at 300ºC 2) | 0,088 | 0,088 | 0.189 | 0,083 | 0,089 | 0,089 |
Density after calcination [g / cm3] | 2,4 | 1.9 | 3.3 | 2,4 | 2,8 | 2,8 |
Mass loss after heating to 750ºC [%] | <0.1 | <0.1 | <0.1 | <0.1 | <0.1 | <0.1 |
Emissivity (black) | 0.92 | 0.9 | 0.32 | 0.98 | 0.98 | |
Porosity [%] | <0.1 | <0.1 | <0.1 | <0.1 | <0.1 | <0.1 |
Resistance to thermal shock [ºC / sec] | > 600 | > 500 | > 200 | > 500 | > 800 | > 780 |
Adhesion | ||||||
to metal [MPa] 3) | 13 - 15 | 13 - 15 | 11 - 13 | 12-14 | 13-14 | 11 - 13 |
to ceramics [MPa] 3) | > 40 | > 40 | 28 - 45 | > 40 | > 40 | 28 - 45 |
Abrasion resistance | ||||||
at 20ºC [ml] 4) | 3.7 (100%) | 3.6 (100%) | 1.5 (100%) 6) | 4.6 (100%) | 3.8 (100%) | 3.9 (100%) 6) |
at 1000ºC [ml] 4.5) | 3.5 (106%) | 3.6 (105%) | 1.2 (125%) 6) | 4.4 (105%) | 4.6 (105%) | 4.6 (125%) 6) |
Solid Composition Component | ||||||
Apparent (bulk) density [g / cm3] | 1.43 | 1.27 | 3 | 1.35 | 1.65 | 1.68 |
Appearance | Light green powder | Light green powder | Black powder | Light gray powder | Dark green powder | Gray green powder |
1) at 18ºC 2) on hot red wire 3) CSN EN 24624 4) ASTM C 704 - 94 5) ∆T = -980ºC 6) Start at 700ºC, ∆T = -680ْ C
Fluid parts
Part | A | B | Water |
Appearance | clear viscous liquid | clear viscous liquid | clear liquid |
pH | > 10.7 | > 11.0 | 7 |
Viscosity (4mm) [s] 1 | 18.3 | 12.3 | 10 |
Density [g / cm3] | 1,2 | 1.12 | one |
Solids content (%) | 32,5 | 32 | 0 |
1) at 18ºC
Initially laying in the process of designing tube furnaces the most advanced engineering solutions, designers provide the highest possible (at the moment) efficiency. In the process of operation of furnaces over time occurs:
- moral aging of design decisions,
- physical wear of structures,
- increase in specific fuel consumption,
- increase in gross emissions of harmful substances.
As a result, the operation of the furnace deteriorates, and the efficiency decreases sharply.
Usually, the total amount of heat (Q floor) received by the furnace between the radiant and convection chambers is distributed as follows:
Qrad = 0.75 * Q floor | Qcon = 0.25 * Q floor |
Heat transfer in furnaces at temperatures above 700 ° C is carried out mainly by radiation. In order to intensify radiant heat transfer and increase the efficiency of tube furnaces (both operating and newly designed) for oil refining, petrochemicals and energy, a technology has been developed for applying ceramic high-emitting ceramic coatings (VIP) on refractory surfaces and metal pipes.
Previously it was believed that the degree of blackness of all surfaces in the furnace is Ɛ = 0.85 and was a value independent of temperature.
Emissivity (or degree of blackness) - ε shows the ratio of the energy of the thermal radiation of the 'gray body' according to the Stephen Boltzmann Law to the radiation of the 'absolutely black body' at the same temperature. The emissivity of a black body is ε = 1.
Currently, special studies have shown that with increasing temperature the emissivity of refractory materials is reduced and in the temperature range of 700 ° C -1000 ° C is Ɛ = 0,4-0,7
At the same time, the degree of blackness of special coatings on metal oxide increases with increasing temperature and at 1000 ° C reaches Ɛ value = 0.95.
The given degree of blackness of the combustion chamber depends on both radiating surfaces and heat-absorbing pipes, therefore high-emitting ceramic coatings (VIP) with a high degree of blackness should be applied to all surfaces in the furnace.
The flue gases resulting from combustion possess significant emissivity and absorptivity (carbon dioxide (C0 2), water vapor (H 2 0), sulfur dioxide (S0 x), NO x) , but:
- Emission and absorption of gases is in the nature of selective (selective) radiation, i.e., gases emit and absorb energy only in certain wavelength ranges, in the so-called bands located in different parts of the spectrum.
- For rays of other wavelengths outside these bands, the gases are transparent, and their radiation energy is zero.
- The absorption capacity of a gas depends on its partial pressure, temperature, and layer thickness. With increasing density and thickness of the layer, the absorption capacity of the gas increases.
- The width of individual emission bands varies with gas temperature. With increasing temperature, the width of the bands increases, and the absorption capacity decreases, because gas density decreases. But as a result of increasing temperature, the radiation energy increases.
For carbon dioxide and water vapor, the following bands are most important:
Carbon dioxide CO 2 | Water vapor N 2 O | |
1st lane | l = 2.36 ... 3.02 μm | l = 2.24 ... 3.27 μm |
2nd lane | l = 4.01 ... 4.80 microns | l = 4.80 ... 8.50 μm |
3rd lane | l = 12.5 ... 16.5 μm | l = 12.0 ... 25.0 μm |
- Mono- and diatomic gases (N 2 , O 2 ) are incapable of radiation and absorption of radiant energy; in practice, these gases are transparent to diathermy for thermal rays.
- In gases, radiation and absorption always proceeds in volume.
- Solids emit and absorb energy from the surface layer.
- Solids have continuous emission spectra: they emit (and absorb) radiant energy of all wavelengths from 0 to ∞.
An increase in the degree of blackness of the lining leads to an increase in the absorption of heat from flue gases and the emission of this energy in the continuous spectrum, which in turn leads to an increase in the absorption of re-emitted heat by the pipes.
Experiments conducted on industrial furnaces showed that at a given temperature of the product in the furnace tubes:
- the temperature of the flue gases at the exit of the radiation chamber decreases.
- the temperature of the flue gas from the convection chamber decreases.
- specific consumption of equivalent fuel is reduced,
- emissions of harmful substances into the atmosphere (greenhouse gases) are reduced.
- uneven temperature around the circumference of the pipe is reduced.
- maximum pipe wall temperature decreases
- the likelihood of coke formation is reduced.
- the surface oxidation rate decreases sharply
- thermal shock resistance increases
- the period between coke burning increases (for high-temperature furnaces)
- increases the mechanical strength of the lining and its service life
- resistance to aggressive flue gases (SOx) increases
- the efficiency of the furnace increases.
- increases the reliability of operation of furnaces;
- VIP service life is from 4 to 8 years depending on the fuel used
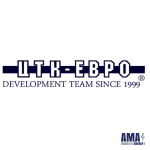