Complex of non-Destructive Testing UNKT-500
The complex provides the following control operations:
- identification of defects of various orientations on the outer and inner surfaces, as well as in the thickness of the metal (delamination, sunsets, sinks, pits, etc.) in accordance with GOST 633-80, GOST R 52203-04, GOST R 53366-2009, API ;
- wall thickness measurement and breakdown by tolerances (classes) according to RD 39-136-95, RD 39-013-90 or API RP 7G;
- determination of compliance of controlled pipes to this strength group;
- marking of defective places on the pipe indicating the coordinates of the defects;
- management of related equipment functionally associated with the complex;
- recording, processing and accounting of information on the above listed pipe control operations.
Technical specifications:
- The conditional sensitivity of the installation complies with the requirements of GOST 633-80, GOST R 52203-04, GOST R 53366-2009, API;
- The range of measured thicknesses is 3 ... 30 mm;
- The error in measuring wall thickness is ± 0.1 mm;
- The error in determining the coordinates of the defect is ± 50mm;
- Uncontrolled section of the end of the pipe - 50 mm;
- The control speed is 0.4 m / s, which ensures hourly productivity of at least 40 pipes per hour in automatic mode.
Performance Parameters:
- The operating mode of the complex is automatic, continuous in accordance with the operating mode of the operating organization;
- Changeover time to another pipe size - not more than 20 minutes;
- Attendants - 1 operator;
- Overall dimensions of the UNKT-500 installation - 4000 × 1200 × 2000;
- Overall dimensions of the complex with a vehicle - 29900 × 1200 × 2000;
- Climatic modification of the complex - UHL-3;
- The installation should be operated indoors at an air temperature of +5 ... .. + 35º C.
Energy requirements:
- Electricity - 220 / 380V, 50 Hz, installed power - 15 kW;
- Compressed air pressure of 0.5-0.6 MPa, pollution class 11 according to GOST 17433-80.
Parameters of controlled pipes:
- Diameters of tubing - 60 ÷ 114 mm;
- Wall thickness - 4.0 ÷ 15 mm;
- Length - 5.5 ÷ 12.5 m;
- Strength groups - D, K, E, L, M, P;
- Controlled pipes must be cleaned (washed). Organic contaminants with a thickness of more than 0.1 mm are not allowed on the outer surface. The total area of contamination on the pipe should not exceed 20% of the entire surface of the pipe;
- One screwed-in coupling is allowed on the pipe.
The composition of the CNTT complex is 500:
- Ultrasonic control module for longitudinal and transverse defects, longitudinal weld of electric-welded straight-seam tubing;
- Module for ultrasonic control of pipe wall thickness;
- Module of magnetic induction monitoring of discontinuities and pitting corrosion;
- Demagnetization module;
- The control module of the strength group “Sortoscope 4;
- Software and computer complex (PVC);
- Defect marker;
- Module for manual control of the landing zone, the castle part (option for BT);
- Transport system:
- input roller table;
- live roll;
- loading and unloading pavers;
- Set of measures of non-destructive testing "KMNK-500".
Brief description of the control process
Pipe control is performed automatically. The pipe is loaded from the workshop rack to the input roller table and through the roller table with rotation it enters the magneto-induction control module, ultrasonic defectoscopy module, ultrasonic thickness gauge module, demagnetization device, Sortoscope-4M strength group determination device, and enters the output roller table. At the output roller table, the flaw detector puts marks on the pipe in the places of defects. Based on the results of the control, the computer complex makes a decision on the suitability of the pipe and the pipe is unloaded on the shop rack.
The operator has the ability to visually monitor the entire control process and, if necessary, intervene to make a decision.
The magneto-induction control module ensures the detection of continuity defects in the metal, through holes, and pitting corrosion. Parameters of detected defects in accordance with the requirements of GOST 633-80, GOST R 52203-2004.
The ultrasonic flaw detection module is performed by the traditional proven immersion method and allows you to identify defects of various orientations in the form of marks, cracks, sunsets, delaminations, shells in the thickness of the metal and on the surface
The ultrasonic thickness gauge module provides direct measurement of pipe wall thickness with an accuracy of ± 0.1 mm over the entire pipe surface.
The demagnetization device provides demagnetization of the pipe material to standard values.
Determination of the strength group of the material is performed on the installation "Sortoscope-4" eddy current method.
The flaw detector, on command from the computer complex, puts marks on the pipe in the places of defects. The accuracy of determining the coordinates of defects is ± 50 mm.
The sensitivity of the control is adjusted using non-destructive testing with artificial defects (CMC) in accordance with the requirements of GOST 633-80 and GOTS R 52203-04. KMNK-500 are included in the delivery and are accompanied by verification certificates issued by the Samara Center for Standardization and Metrology.
Distinctive features.
Provides high stability and reliability (98%) of the complex due to:
- applying a combination of several control methods that are targeted to the control objects (defects) inherent in these methods;
- multiple zone overlap during ultrasonic testing (8 thickness gauges and 8 flaw detectors), as well as the use of a new signal supply and processing system developed by the well-known company SPC KROPUS LLC;
- the use of highly sensitive magnetic induction control sensors manufactured using the NANO technology for applying a magnetically sensitive layer.
The sensors of magneto-induction control are located equidistantly relative to the pipe body with a gap of up to 5 mm, contact with the pipe body has a housing in which the sensors are located, so wear of the sensors themselves is excluded. Guaranteed sensor life - 1 year.
The modular principle of channel construction ensures their independence, which allows for high-speed operation of the system and the implementation of various signal processing modes in each channel with a sending frequency of up to 10 KHz.
The scanning devices (carriages) of the modules are made floating, which ensures their self-positioning relative to the surface of the pipe, thereby maintaining a constant position of the sensors, which is fundamentally important for the clear detection and fixing of defects.
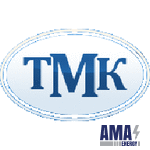