CNC Metalworking Centers models GA-2000 / GA-2600 / GA-2800
Key Specifications
Model | GA-2000 | GA-2600 | GA-2800 |
Key technological capabilities | Specifications | ||
The maximum diameter of the installed product, mm | 580 | ||
Maximum turning diameter, mm | 350 | ||
Maximum turning length (GA-2000-300 / GA-2000 / GA-2000L), mm | 309/624/1204 | 291/606/1186 | 260/575/1155 |
Maximum weight of the installed product, kg | 170 | 230 | 250 |
Diameter of a cartridge, inch | Ø8 " | Ø10 " | 10 "(Big-Bore) |
Max bar diameter, mm | Ø51 | Ø65 | Ø77 |
SPINDLE | |||
Hole in the draft pipe, mm | Ø52 | Ø66 | Ø76 |
Spindle bore, mm | Ø66 | Ø76 | Ø90 |
Diameter of spindle bearings, mm | Ø100 | Ø120 | Ø130 |
Hydraulic cylinder, inch | 8" | 10" | 10 "(Big-Bore) |
Spindle end | A2-6 | A2-8 | A2-8 |
Spindle Drive Motor Model | Fanuc alpha iP22 / 6000 | ||
Spindle drive motor power kW | 11 (nominal) / 15 (30 min) / 18 (peak) | ||
Spindle motor transmission | Belt | ||
Gear ratio | 4: 5 | 2: 3 | 7: 12 |
Spindle rotation speed range, rpm | 48-4800 | 40-4000 | 35-3500 |
Spindle torque (const. / 30 min), N * m | 175/238 | 200/286 | 240/327 |
Dual-mode drive (optional) range switching is carried out by changing the electrical switching of the motor windings | |||
Ranges of speeds of rotation of a spindle (Low), rpm | 20-1200 | 20-1000 | 20-875 |
Spindle speed ranges (High), rpm | 1201-4800 | 1001-4000 | 876-3500 |
Spindle torque (15 min) Low, N * m | 360 | 430 | 497 |
Spindle torque (30 min) High, N * m | 238 | 286 | 325 |
C-axis (optional) | |||
Engine model | AC Servo Motor 0.7 kW, Fanuc alpha 2 / 5000i | ||
Torque, N * m / maximum speed, rpm | 240/33 | ||
X, Z AXIS | |||
Maximum amount of displacement along the X axis, mm | 205 (may vary depending on the installed options) | ||
Maximum displacement along the Z axis, mm | 350 | 650 | 1230 |
Fast movement along the X / Z axes, m / min | 20/24 | ||
Type of guides (sliding) | Hardened, sanded, box type | ||
Range of working gears, mm / min | 1–4800 | ||
X axis drive motor, kW | AC 2.7 | ||
Z axis drive motor, kW | AC 2.7 | ||
Diameter, mm / pitch of ballscrew on X axis | Ø32 / step 6 | ||
Diameter, mm / pitch of ballscrew on Z axis | Ø36 / step 10 | ||
Force (Const.) On axes X / Z, kg | 962 | ||
Turret | |||
Number of turret positions | 12 standard (10 optional) | ||
Drive motor (drum rotation) | Electric drive (AC Servo Motor) | ||
Tool change speed, sec | 0.2 position connection / 0.5 rotation 180 ° | ||
Positioning Accuracy / Repeatability | ± 0, 00069 ° / ± 0, 00027 ° | ||
Tool holder section, mm | 25 * 25 | ||
The maximum diameter of the shank of the axial tool, mm | Ø40 | ||
REVOLVING HEAD WITH TOOL DRIVE (OPTIONAL) | |||
Number of turret positions | 12 | ||
The number of drive positions turret | 12 | ||
Tool drive motor | 4.5 kW, 22 N * m, electric drive | ||
Tool change speed, sec | 0.2 adjacent positions / 0.5 rotation 180 ° | ||
Tool holder section, mm | 25 * 25 | ||
The maximum diameter of the shank of the axial tool, mm | Ø40 | ||
Power Tool Collet Size | ER32 | ||
Range of rotation speeds, rpm | 40 - 4,000 | ||
REAR BATTERY (OPTIONAL) | |||
Pinoli cone type | KM4 (integrated rotating unit) | ||
Pinole diameter / pinole stroke, mm | Ø 70/150 | ||
Moving the tailstock GA-2000-300 / GA-2000 / GA-2000L, mm | Fixed / 550/1140 | ||
Programmable movement of the tailstock / tailstock housing | Yes / Yes (not possible for GA-2000-300) | ||
FINISHED PARTS CATCH (OPTIONAL) | |||
The maximum diameter of the part, mm | Ø77 | ||
Maximum part length, mm | 150 | ||
TOTAL INFORMATION | |||
Positioning accuracy / repeatability, mm | ± 0, 005 / ± 0, 003 | ||
Standard (basic) CNC system | Fanuc oi-t | ||
Voltage / power | AC 200/220 + 10% to 15% 3-phase / 26 kW | ||
Hydraulic power tank capacity, l | thirty | 40 | 40 |
Coolant tank capacity, l | 200 | ||
Net weight (GA-2000-300 / GA-2000 / GA -2000L), kg | 3,500 | 4,000 | 4,600 |
Design Features
GA-2000 is a metal-working center of a classical layout with Z axis guides located in a horizontal plane. The inclined arrangement of the X axis guides provides high rigidity and optimal chip evacuation. Belt transmission in the drive transmission of the drive of the main movement allows you to fully realize the capabilities of the engine both in speed and in torque. This combination of design solutions allowed the GA-2000 series to achieve optimal values in the price / quality ratio and satisfy the needs of a wide range of customers.
The bed, headstock and caliper parts are solid cast from specialized cast iron of the Meehanite class (Taiwan) and have developed finning. The headstock is mounted on the bed by means of a bolted connection. Cast elements undergo artificial and natural aging. The total time of the artificial aging process is 32 hours.
Applied artificial aging technology:
- heating for 2 hours to 400 ° C, followed by exposure for 1 hour;
- heating for 3 hours from 400 to 580 ° C;
- exposure at a temperature of 580 ° C for 4.5 hours;
- cooling at a speed of 50 ° C / hour - from 580 to 430 ° C;
- natural cooling from 430 ° C to ambient temperature.
After artificial aging, all castings undergo natural aging within 3-6 months.
The machining of cast components is performed on OKUMA, Mitsui Seiki, YASDA milling machines. The slideways along all axes are hardened to HRC 53–55 to a depth of 1.5–2 mm.
The covering surfaces of the guides and the mating planes of the main units undergo the scrapping procedure. This ensures high accuracy, rigidity and provides the best lubrication condition for moving parts.
The slide carriages are coated with anti-friction and wear-resistant Turcite-B material, which provides the pair with no Stick-slip effect (jump effect), which guarantees high accuracy of movement and repeatability of positioning of the working bodies and increases the service life of the machine components.
The processing of critical openings of the headstock is carried out on a YASDA precision boring machine in a thermostatically controlled room. After assembly, the headstock arrives at the test bench, where temperature, noise and vibration are monitored for 24 hours under various modes and loads, and the results are entered into the database.
Ball screw pairs (ballscrews) on both linear axes are pre-assembled and have direct drive from the engine through the coupling. Ball screw pitch errors are measured using a laser system manufactured by Agilent Technologies (USA), corrective values are entered into the memory of the CNC system.
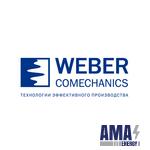