MCV Series Column Vertical Milling Machining Centers
The possibility of installing tilting tables (4–5 axis) significantly expands the processing capabilities of the machine. Machines of this range are delivered in standard containers, which positively affects the cost.
Machines of the MCV – 1250… MCV – 2600 models are designed for machining medium and large parts both in fairly severe cutting conditions and during finishing, combining in their design the optimum performance of the main drive power, high rigidity and accuracy. This is achieved through the use of a two-stage gearbox in the spindle drive, sliding guides with a large coverage area in all coordinates, and a bed of high rigidity, calculated using the finite element method.
Key Specifications
Model | MCV-720 | MCV-860 | MCV-1020BA | MCV-1020A | MCV-1060 | MCV-1200BA | MCV-1200 |
Table Size (LxW), mm | 950x560 | 950x550 | 1300x660 | 1300x660 | 1200x580 | 1300x640 | 1300x640 |
X / Y / Z axis movements, mm | 720/460/510 | 860/550/550 | 1020/550/560 | 1200/600/500 | |||
Maximum load on the table, kg | 500 | 800 | 1000 | ||||
Quick movements along the X / Y / Z axes, m / min | 24/24/18 | 40/40/30 | 30/30/20 | 20/20/18 | 40/40/30 | 30/30/18 | |
Tool shank | BT40 | BT50 / BT40 | BT40 | ||||
Maximum spindle rotation speed, rpm | 8000 (opt. 10000, 12000, 15000) | BT50: 5000 BT40: 6000 | 8000 (opt. 10000, 12000, 15000) | 10000 (12000, 15000) | |||
Power of the main engine (nominal / 30min), kW | 7.5 / 11 5.5 / 7.5 | 5.5 / 7.5 | |||||
Tool magazine (number of positions) | 16 (24, 30) | 24 (30.32) | 16 (24,30, 32, 40) | 25/20 (30.32.40) | 24 (30.32.40) | ||
Net weight kg | 4400 | 5400 | 6000 | 7000 | 6000 | 7500 |
Model | MCV-1250 (B) | MCV-1450 (B) | MCV-1680 | MCV-2100 (B) | MCV-2600 (B) |
Table Size (LxW), mm | 1400x820 | 1600x800 | 1800x850 | 2300x970 | 2600X970 |
X / Y / Z axis movements, mm | 1250/650/700 | 1450/750/750 | 1680/850/800 | 2100/850/760 | 2600/850/760 |
Maximum load on the table, kg | 1500 | 2000 | 2500 | 3000 | 3000 |
Quick movements along the X / Y / Z axes, m / min | 20/20/12 | 20/20/12 | 36/36/20 | 10/10/8 | 10/10/8 |
Tool shank | BT50 / BT40 | ||||
Maximum spindle rotation speed, rpm | BT40: 8000 (10000, 12000, 15000) BT50: 6000 (10000) HSK50: 10000 | ||||
Power of the main engine (nominal / 30min), kW | BT50: 11/15 BT40: 7.5 / 11 (15) | BT50: 11/15 BT40: 11/15 | BT40: 7.5 / 11 (11/15) | BT50: 15 / 18.5 BT40: 11/15 (15 / 18.5) | |
Tool magazine (number of positions) | 24.32.40 | 30.32.40 | |||
Net weight kg | 10500 | 14500 | 15500 | 18000 | 19000 |
Design Features
The bed, column, headstock and caliper parts are all-cast from specialized cast iron of the "Meehanite" class (country of manufacture - Taiwan), have developed finning. The column is mounted on the bed by means of a bolted connection.
Cast elements undergo artificial and natural aging.
The total time of the artificial aging process is 32 hours.
After artificial aging, all castings undergo natural aging within 3-6 months.
Applied artificial aging technology:
- heating for 2 hours to 400 ° C, followed by exposure for 1 hour;
- heating for 3 hours from 400 to 580 ° C;
- exposure at a temperature of 580 ° C for 4.5 hours;
- cooling at a speed of 50 ° C / h from 580 to 430 ° C;
- natural cooling from 430 ° C to ambient temperature.
The machining of the cast components is performed on OKUMA, MitsuiSeiki milling machines, followed by grinding on WaldrichCoburg machines at DAHLIH's own production facilities.
Slide guides along the Z axis are hardened to HRC 53-55 to a depth of 1.5 - 2 mm. (The guides of the X, Y axes are rolling.)
The covering surfaces of the guides and the mating planes of the main units undergo the scrapping procedure. This ensures high accuracy, rigidity and provides the best lubrication condition for moving parts.
The covering surfaces of the Z-axis guides are coated with anti-friction and wear-resistant material “Turcite-B”, which ensures the operation of the pair without the Stick-slip effect (jump effect), which ensures high accuracy of movement and repeatability of positioning of the working bodies and increases the service life of the machine components.
The critical holes of the headstock are processed on a YASDA precision boring machine in a thermostatically controlled room. After assembly, the headstock arrives at the test bench, where temperature, noise and vibration are monitored for 24 hours under various modes and loads, and the results are entered into the database.
An active liquid spindle thermal stabilization system is included in the basic package.
Ball screw pairs (ballscrews) on all axes are assembled with a preload, and have direct drive from the engine through the coupling. Ball screw pitch errors are measured using a laser system from Agilent Technologies (country of manufacture - USA), corrective values are entered into the memory of the CNC system.
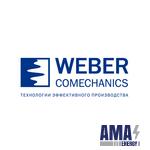