Fuel Briquettes Plant - 1...1.5 t/h Multi-Raw Materials
(设备/材料)
描述:
Complete plant for production of fuel briquettes with the capacity of 1 ... 1.5 t/h. Raw materials: any bulk, straw in rolls and bales, large-piece wood waste and pulpwood. Logs, slabs, etc. wood waste are fed to the chipping machine (18) by the conveyor (19). From it, the chips go to the conveyor (20) and then to the mechanized warehouse “moving floor” (1). Straw in rolls goes to the receiving table (22), then goes to the roll straw chopper (21). The chopped straw is sent by pneumatic transport to the mechanized warehouse “moving floor”. Fine-fraction raw materials are delivered by motor transport (or a loader) and poured onto the mechanized warehouse “moving floor” (1). The stockers of the moving floor have a hydraulic drive and under its action perform reciprocating movements. The blades (“wings”) of the stokers have a wedge-shaped form, therefore, when the stokers move, the raw material is directed to the chain (scraper) conveyor (2) at an adjustable feed rate, then the raw material is fed to the disk separator (3). On it, stones, roots, etc. impurities are separated from the raw material, which fall into a portable container (not shown in the diagram), and the raw material by gravity falls into the loading section of the Drying and Grinding Unit (4). Combustion products from the heat generator (5) are also fed here, and cold atmospheric air is sucked in through the emergency ignition pipe (6) (not included in the kit). Initially, combustion products and cold air are mixed, the mixing proportion is adjusted automatically, which ensures that the set temperature of the coolant is maintained. Then the coolant is mixed with wet raw materials and sucked into the Drying and Grinding Unit (4). In it, the raw material is crushed and then dried, rising in the flow of the coolant to the dynamic classifier, located in the head section of the Drying-Crushing Unit. The dynamic classifier, the frequency of which is set from the control panel (15), passes small and dry raw materials, and returns large and wet particles of raw materials to the rotor of the Unit, this process is repeated until the required humidity and degree of grinding of the raw material is obtained (more details). The crushed and dried raw material (from this point on it is customary to call it flour) is sucked into the sedimentation cyclone (8) due to the vacuum created by the smoke exhauster. In the cyclone, the flour settles due to centrifugal force and moves downwards, and the spent coolant is thrown into the smoke stack (16). From the cyclone, the flour is fed through a lock valve into a screw or chain conveyor (9), then goes to the hopper of the briquette press (10). Inside the hopper there is a device preventing the flour from caking. From the hopper the flour is sent to the briquette press (11) by a screw feeder with an adjustable feed rate. In the press the flour first enters the pre-pressing chambers, from where it is fed by two counter-directed screws to the pressing chamber. In the pressing chamber the flour is pressed by a movable piston (piston) into a conical fixed matrix, where under the action of high pressure a continuous briquette (hereinafter for simplicity referred to as "briquettes") is formed. The briquettes coming out of the press have a high temperature and are fragile, so they are sent to the briquette tunnel cooler (12). During the cooling process the humidity of the briquettes decreases due to the evaporation of moisture, and physical and chemical changes occur in them. As a result, they acquire the necessary hardness, humidity and temperature. Moving along the cooling tunnel, which in this case is also a conveyor, the continuous briquette passes through a metal detector (13) and enters an automatic saw (14), where it is cut into briquettes of a given length. Then the briquettes are sent to the packaging section and the finished product warehouse (not shown). The heat generator in this configuration can be loaded with fuel both manually (through the door) and automatically - from the fuel bunker (7). The fuel bunker can be replenished automatically (optional) by returning part of the flour from the sediment cyclone (8) using the pneumatic transport system (17). Optionally, the fuel bunker can be replenished by an additional conveyor from the raw material warehouse or a separate fuel warehouse (not shown).
概观:
PARAMETER NAME | MEANING |
Dimensions | |
Length, m | 41.5 |
Width, m | 22.0 |
Height, m | 8.7 |
Electrical power | |
Connected electrical power, kW | 320 |
Dimensions of the room | |
Length, m | 28.5 |
Width, m | 15.0 |
Height, m | 6.0 |
Weight | |
Weight, kg | 32 850 |
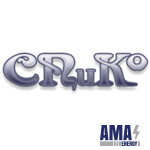
OOO "SP and KO"
地点: 180021, Pskov, Industrialnaya st. 11
主要产品/服务: Equipment for biofuel production